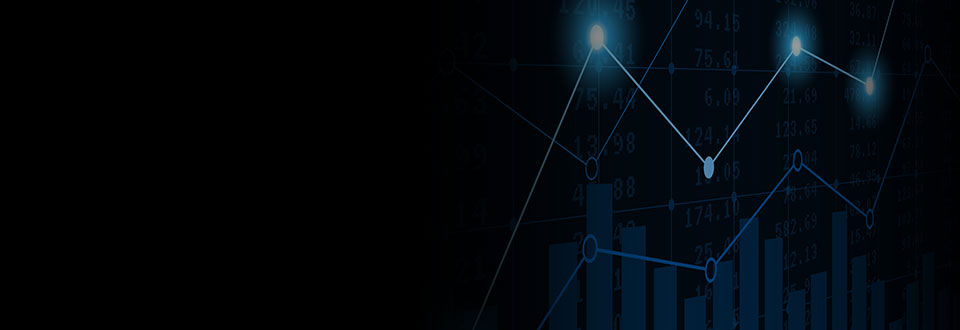
鋳物製品の調達コストを
削減するための
業界最新トレンド2025
鋳物製品の調達コスト削減するためには、最新の業界トレンドを活用した戦略的なアプローチが求められます。
本記事では、調達コストを抑えるための鋳物業界の最新のトレンドと、神栄の戦略について紹介します。
デジタル技術と自動化の導入
近年、鋳造業界ではデジタル技術や自動化の導入が進んでいます。
例えば、3Dプリンターを活用した試作品の内製化により、外注費の削減や無駄のない設計で生産性の向上が実現します。
また、IoTやAIを活用した生産管理システムの導入により、リアルタイムでの生産状況の把握や需要予測の精度向上が可能となり、在庫コストの削減や生産効率の向上につながります。
神栄ではIoTネットワーク構築により納期遅延を防ぐべく、日本-供給元(ベトナム・タイ)で生産計画や船積み管理などを随時共有し、リアルタイムで生産体制・物流の最適化を図っています。
また、協力工場では自動造型機を導入し、品質の安定化・適切な人員配置の体制を整えています。
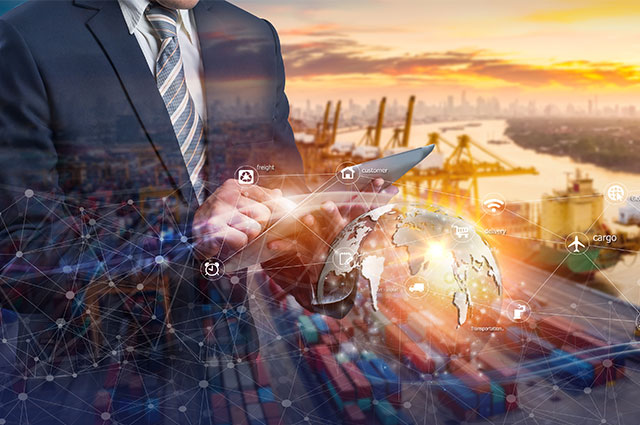
原材料の効率的な活用
鋳鉄部品のコスト構造において、原材料費は大きな割合を占めます。
そのため、原材料の効率的な調達がコスト削減の鍵となります。
削減の具体例として、3Dを活用した部品設計で精度を向上させ、加工代を出来る限り少なくし、必要最小限のロスのない材料で加工を行うことで、無駄な加工時間を省き、材料費も大幅に削減することが可能です。
さらに、複数のサプライヤーとの長期的なパートナーシップを築くことで、鋳造技術の移転・向上による品質の安定化を図ることも重要です。
神栄の協力工場があるベトナム・タイ国内の鋳物の原材料は主に輸入に頼っています。
その為、原材料費が高くなりがちですが、神栄の現地協力工場ではインドや中国などのベトナム・タイの隣接地域から原材料を調達し、輸送費を抑えることで、原材料費の低減を実現しています。
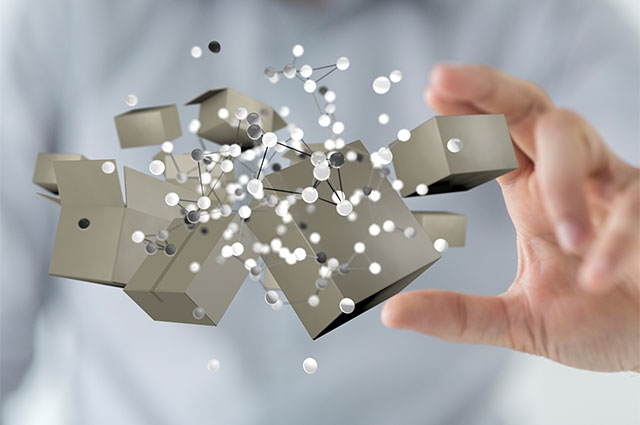
生産工程の最適化と省エネルギー化
生産工程の効率化や省エネルギー化も、コスト削減に直結します。
例えば、外注作業を減らし、自社で一貫生産体制を整えることで、モノの行き来をなくすことで、生産工程を最適化できます。
また、日中に比べて電力が安価な夜に注湯を増やすことで、エネルギーコストを削減することが可能です。
神栄の協力工場でも夜間の工場稼働時間を増やし、エネルギーコストを削減しています。
また、各工程の専門会社からトップレベルの作業員を派遣し、工程ミスを抑えながら、協力工場内での一貫生産体制の構築を行っています。
さらに、出荷時には、自社用パレットを作成し、輸送コンテナ内の余白を出来るだけなくすことで、物流の最大限活用による輸送コストの抑制だけでなく、環境への配慮を行っています。
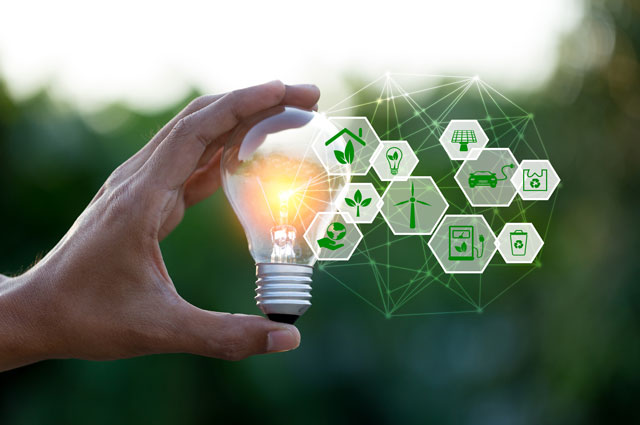
サプライチェーンの強化とリスク分散
サプライチェーン全体の効率化とリスク分散も重要なポイントです。
複数のサプライヤーを活用することで、供給不安や品質問題のリスクを分散することで供給責任を果たすことが出来ます。
現在のベトナムでは11年前と比べ、技術水準が上がっていますので、例えば鋳物とゴムを熱溶着するなどの対応も可能です。
様々なサプライチェーンとの取引を行うことで、多種多様の製品製造が可能になります。
神栄では新技術の導入にも、敏速かつ柔軟に対応し、日本品質を維持したまま、工場のレベルアップを図っています。
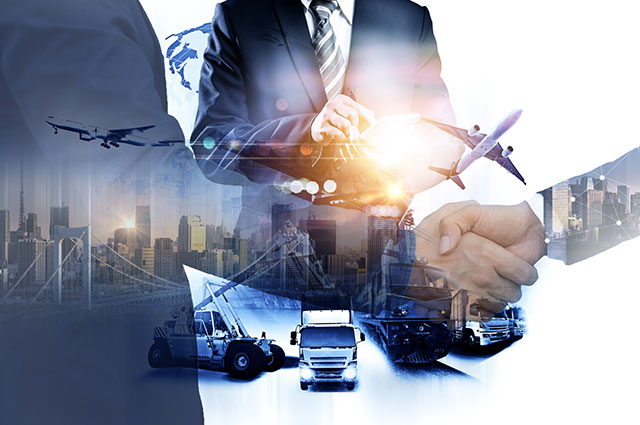
環境への配慮と持続可能な取り組み
ベトナムでは、日本でいう環境省のような機関が、定期的な工場への視察・監査を行うことで、従業員の安全衛生管理体制が向上しています。
具体例として、鋳造工場内では多くの煤塵が発生しますが、作業員の作業環境向上のために、工場内に集塵装置の設置を行ったり、換気頻度を上げたりの対応が行われています。
また、省エネルギー設備の導入により、環境負荷の低減とコスト削減を両立することが可能です。
神栄の協力工場にも、集塵装置や適切な排気ダクトを設置し、従業員の作業環境向上を図っています。
また、生産計画や船積み管理などの最適化、コンテナ内に隙間なく商品を積み込むこと等、コンテナ輸送の最大限の活用により、環境に配慮した取り組みも行っています。
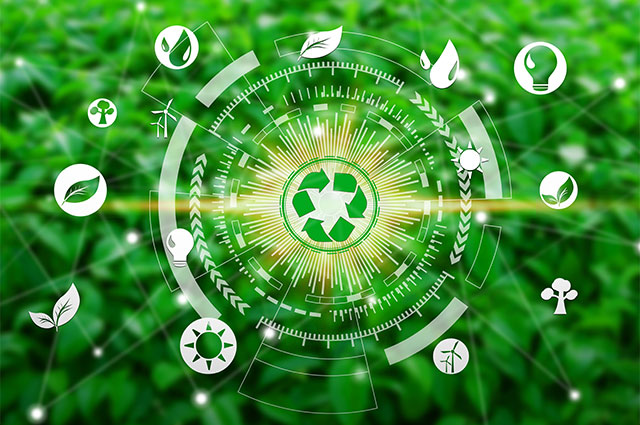
その他の神栄の取り組み
神栄は、40年以上の実績を持つ鋳物・金属製品の調達のプロフェッショナルとして、東南アジアからの戦略的な調達を行い、品質を維持しながら調達コストの削減を行っています。
CHINA+ONE(チャイナプラスワン)戦略
中国に依存する調達先を多様化する戦略の一環として、「CHINA+ONE(チャイナプラスワン)」をスローガンに掲げ、タイやベトナムからの鋳物調達を提案。生産拠点の分散化によるリスクヘッジを行っています。
現地の優れた協力工場と強固なパートナーシップを築き、日本の品質管理手法の現地への定着を実施。品質とコストの両面で競争優位性を確保しています。
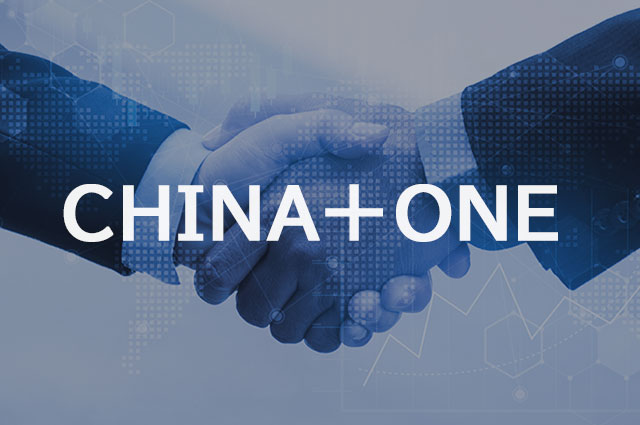
戦略的な製造拠点の選択
ベトナム北部10社以上、南部3社、タイ1社の協力工場ネットワークを構築しています。
製品特性に応じた最適工場へ生産を委託し、地域特性を活かすことで、製造コストの最適化を実現しています。
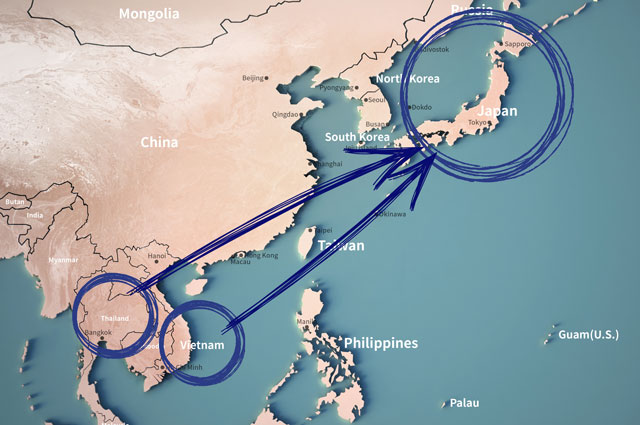
効率的な混載輸送システム
定期輸送体制を整え、最小ロット300KG(応相談)からの混載対応が可能。
また、小ロット・多品種生産の対応を実施し、コストを抑えつつ、柔軟な輸送体制を整えています。
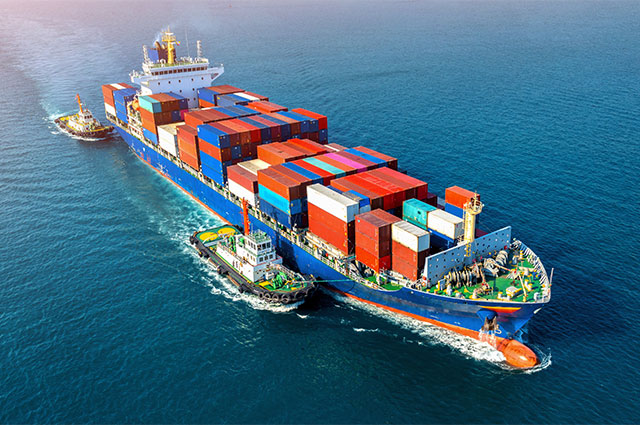
一貫生産体制の構築
現地品質管理体制の確立
日本人技術者による定期的な工場監査による歩留まり、不良発生の防止。
また、現地スタッフ常駐管理体制による不具合への即時対応、出荷前検査による不良品の流出防止することで高品質を維持しつつ、管理コストを抑えています。
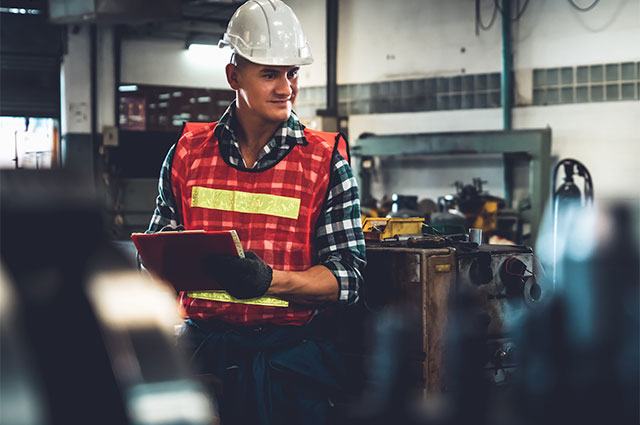
現地の技術サポートの徹底
2025年3月で、神栄とベトナムの協力工場は取引開始から12年目を迎えます。
過去30年間で、中国での鋳物技術は飛躍的に向上したと言われていますが、神栄は中国での鋳物市場の成長を注視し、最新のトレンドを常に追従。
11年前の当時、鋳物の技術水準が低かった状態のベトナム協力工場に日本品質の理解と鋳造技術を定着させました。
5Sの徹底など基本的なことから、最新技術の導入等を通して、今後も現地と協力し、鋳物市場を牽引して参ります。
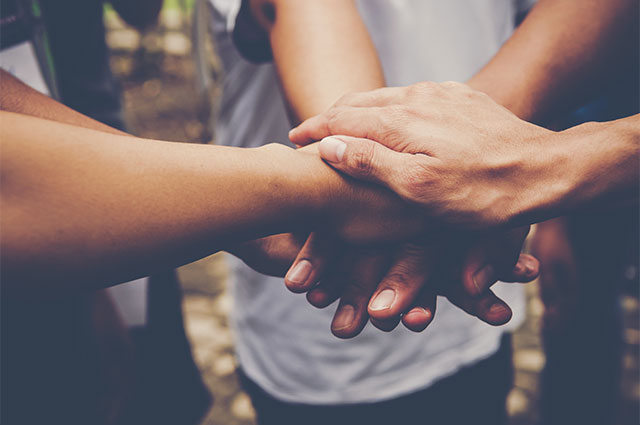
まとめ
調達コストを抑えるため、鋳物業界では、下記の対策が行われています。
- IoT・AI生産管理システムの活用による生産状況のリアルタイム把握・需要予測精度向上・在庫コスト削減。
- 3Dよる設計精度向上による加工代削減・材料費削減。
- サプライヤーとの長期パートナーシップ連携による品質の安定化。
- 夜間の工場稼働率を上げることによるエネルギーコスト削減。
- 複数サプライヤー活用による供給障害・品質問題のリスク分散。
- 作業環境改善による安全衛生管理の向上。
神栄では、以下の対応を行い、品質管理を徹底しつつ、調達コストの抑制を実現しています。
- 中国依存を減らし、タイ・ベトナムなどアジア方面からの調達を推進。(CHINA+ONE(チャイナプラスワン))
- IoTネットワーク構築により、日本とベトナム・タイで生産計画・出航管理をリアルタイム管理。
- 製品仕様に応じた最適工場への生産委託で、各工場の強みを活かすことで、高品質と製造コストを最適化。
- 混載便の定期輸送体制を整え、小ロット・多品種生産にも対応。また、輸送コンテナの空間最適化による輸送コスト削減・環境配慮。
- 鋳造から加工、塗装までを一貫体制を行うことで、工程間物流コストの削減と品質管理の一元化による効率向上を実現。
- 日本人技術者による定期的な工場監査や現地スタッフ常駐管理体制による不具合への即時対応、出荷前検査による不良品の流出防止。
神栄株式会社は、ベトナム・タイのローカル協力工場から鋳物及び金属製品を輸入販売しております。ベトナムから8年、タイからは約40年以上の輸入実績があり、豊富な経験を持つスタッフを多数有しています。
リスクヘッジとコストダウンとして、ベトナム・タイからの調達をご検討頂きますようお願いいたします。
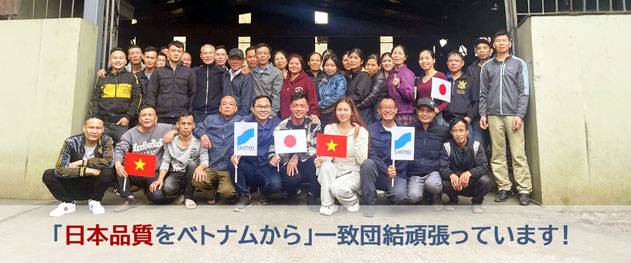
今後も現地スタッフと連携し、引き続き貿易、生産、コスト低減、リスクヘッジなど、鋳物CHINA+ONEでお客様により良いサービスを提供できるように、努力をしていきたいと思いますので、是非、タイ、ベトナムにお越しの際は、現場の視察に足を運んで頂ければ幸いです!